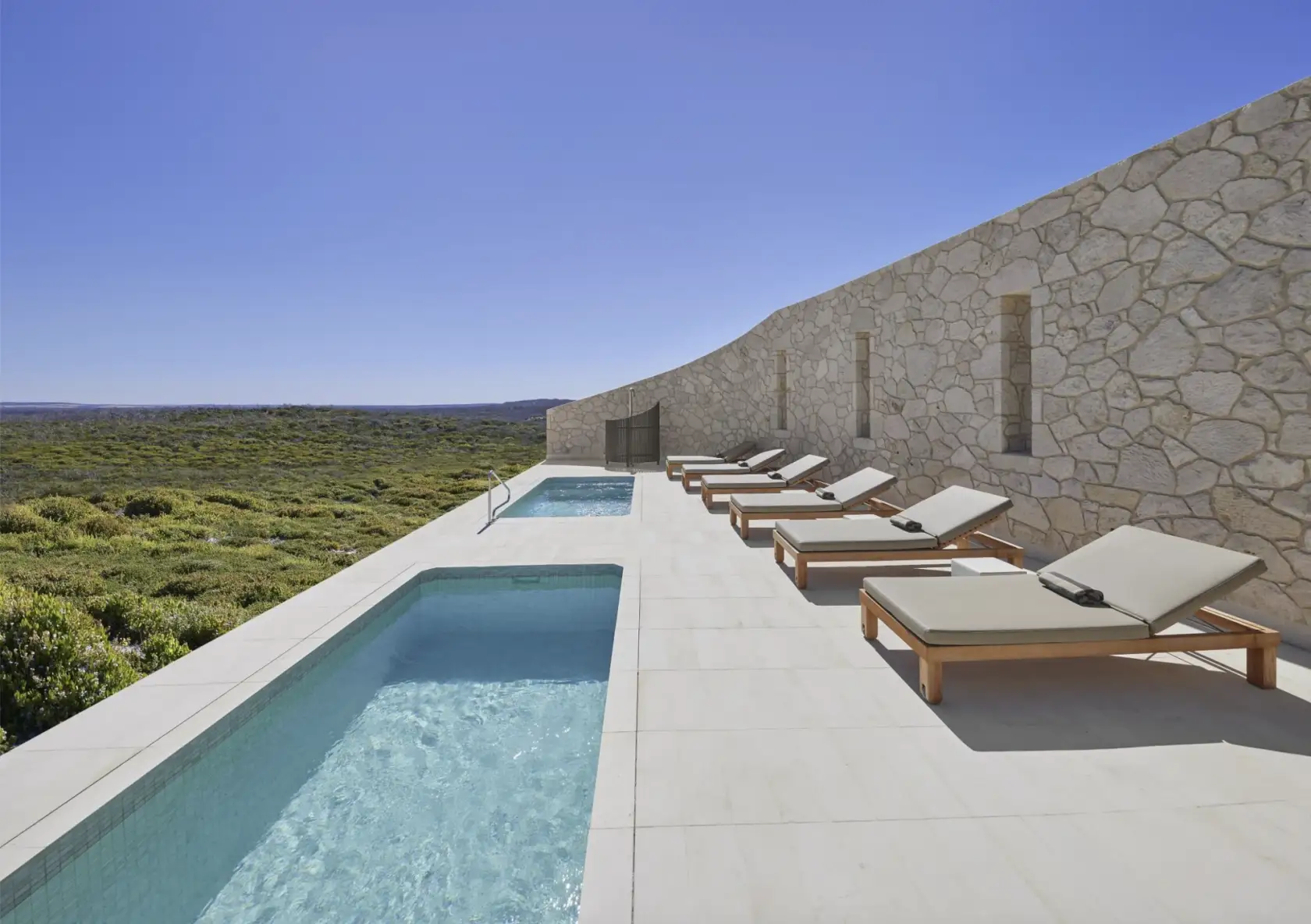
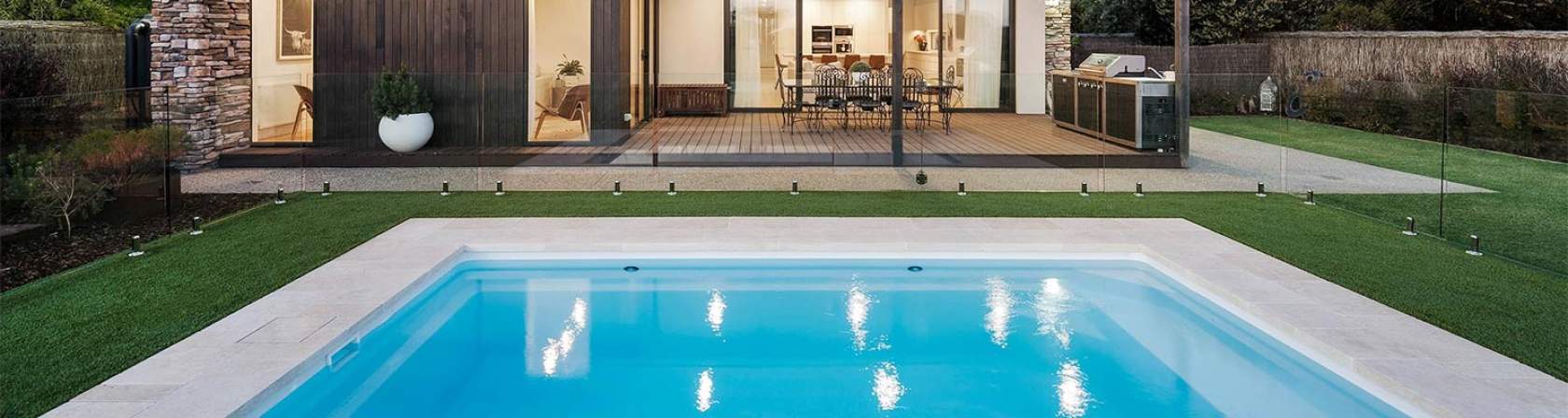
How are fibreglass pools made?
A fibreglass pool is a one-piece pool that comes pre-assembled to your house. A lot of people even call this the giant bathtub among pools. It gets this name because the entire pool comes in one piece from a facility. Fibreglass pools, in other terms, are one-piece swimming pools.
Fibreglass pools bring the best of modern technology and engineering right to your doorstep. They are made in a plant where the pool is assembled layer-by-layer. This process ensures that they are compliant with all the safety standards and you get only the best quality and safest family fun.
These pools are made using a mould. They are then transported to a different site for more layers. They're built up of numerous layers, each of which adds strength and support to the one before it. The layers combine to form a robust, flexible shell that serves as the pool. These pools come in a variety of shapes, including rectangles, circles, and even free shapes, depending on the design you choose. There are different features in the pool as well, such as built-in seats and steps.
How is a fibreglass pool made?
When we say that a fibreglass pool is pre-made and delivered, you are basically approving a design and commissioning the construction. There are 11 steps that go into making a fibreglass pool:
Step 1: Building the plug
The plug is the initial step in constructing a fibreglass pool. It's also known as a pattern, and it refers to the framework that will eventually create the pool. This could be created out of any type of material. Wood, steel, fibreglass, body filler, and primer are popular materials in the industry that are used to make plugs and patterns.
Step 2: Making the Mould
Following the completion of the plug, the next stage is to construct the mould, also known as the shell. The mould is created from the plug. This mould is released from the plug and this allows the mass production of pools in one shape.
Step 3: Getting the gel coat on
Fibreglass pools are constructed from the inside out! The gel coat is the colour scheme that you selected for your pool. It is a coloured resin that is sprayed onto the mould with a spray gun. In order to produce a robust gel finish, this gel coat is applied in three layers. This step is important because if applied incorrectly, the gel coat will be too thin, resulting in scorching of your pool finish. And if it is applied too thickly, it may fracture the initial layer of your pool's surface.
Step 4: Spraying the Vinyl Coating
Following the gel coat, the Vinyl Ester Resin Barrier Coat (water barrier) is applied. The gel coat is semi-permeable, which implies that some water molecules can pass through the gel coat's outer layer. A reaction could occur if the layer beneath is polyester, causing scorching or rusting. This is why, beneath the gel coat, a vinyl ester layer is added. It's a good idea to check with your builder to see whether they employ a manufacturer who uses this layer in their fibreglass.
Step 5: Applying the first layer of chopped fibreglass
Chopped fibreglass is a composite of several materials placed with the use of a fibreglass chop gun. This includes a resin catalyst, as well as fibreglass that has been cut. The combination of these substances improves the pool's strength and longevity. The initial layer of chopped fibreglass is then rolled to ensure that no air is trapped behind it. This layer must be cured.
Step 6: Applying the second layer of fibreglass
The second layer of chopped fibreglass coating is applied now. The pool gains extra strength and stability by adding a double layer of chopped fibreglass coating. Adding this to the pool ensures increased endurance, thus it is always suggested. It is rolled after the second coating has been applied to prevent air from becoming trapped.
Step 7: Placing a Layer of Roving Fibreglass
Following the second fibreglass coat, a layer of woven roving fibreglass is applied. A few producers prefer to use more chopped fibreglass in their products. Whatever type you use, it is highly recommended that you make it as thick as possible.
A lot of attention is paid to certain regions, such as the corners and the point where the pool's wall and floor meet. When a tiny layer of chopped fibreglass is applied to this area, faint spots appear, resulting in minor gel coat damage in the long run. A layer of woven roving can be employed to prevent such an imbalance. A woven fibreglass coating improves the pool's durability and quality.
Step 8: Applying the third coat of chopped fibreglass
A third coat of chopped fibreglass should be applied. After applying the third coat of chopped fibreglass, it is rolled to help avoid air bubbles before being cured (just like the first two layers). To the first and second layers, this adds yet another layer of strength and durability.
Step 9: Applying the Honeycomb Core
Vertical honeycomb core strips are put into the fibreglass pool walls. These are referred to as "ribs" in the industry. These are used to ensure the structural integrity of fibreglass pool walls. This step provides additional strength to the fibreglass. The fibreglass is more flexible and vulnerable to hydrostatic pressure if this stage is skipped.
Step 10: Applying the fourth coat of fibreglass
A fourth coat of chopped fibreglass is applied. After applying the fourth coat of chopped fibreglass, it is rolled to assist avoid air bubbles before being cured. This adds another layer of strength and durability.
Step 11: Applying the fifth coat of chopped fibreglass
This is the final step in the fibreglass pool shell construction process. A final coat of chopped fibreglass is applied to all of the pool shell layers for enhanced strength and longevity. After that, it must be cured and flattened with rollers to help avoid air bubbles.
Following these steps, your pool is ready to be delivered to your house!
Why should I get a fibreglass pool?
Pools made of fibreglass come in a range of designs and sizes. Rectangle, oval, and kidney-shaped are the most prevalent shapes. The usage of readymade moulds limits the amount of personalisation possible. They can be installed in-ground or above-ground. For tiny yards, above-ground fibreglass pools are a fantastic solution. They are also suitable for individuals who wish to avoid the need for excavation and construction. You can personalise your pool by choosing the colour, size, form, and built-in features.
Fibreglass pools can survive the elements, as well as salt, chemicals, and swimmers. When you combine the convenience and low cost of fibreglass with this level of durability, you have a winning combination. And to top it off, you have a range of designs to choose from. It's easy to see why fibreglass pools are becoming increasingly popular.
For more information or further questions, get in touch with our team. On our 'Find a Provider' option, you may find contact information for specialists you can help you with finding the right options for fibreglass pools.